SPONSORED CONTENT
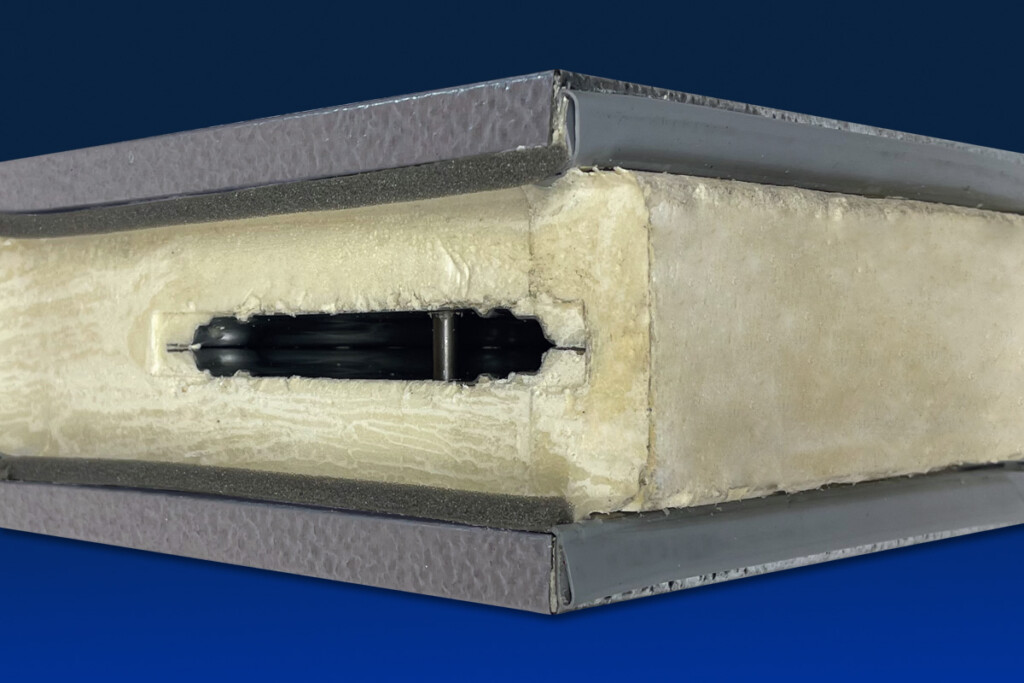
When it comes to walk-in coolers and freezers, probably no factor makes a bigger difference in performance than the panel insulation. There are different types of insulation and they vary in efficiency.
What’s inside the panels determines overall cost of ownership, so it makes sense to go with a manufacturer using the most efficient insulation type.
This article looks at two main insulation materials: polyurethane and polystyrene. While there are advantages and disadvantages with each, one type emerges as the clear frontrunner.
Walk-In Panel Insulation Types
As noted, two of the most common insulation materials are polyurethane and polystyrene. Polystyrene can be further broken into two types: Expanded polystyrene (EPS) or extruded polystyrene (XPS).
EPS is created by expanding small beads of polystyrene inside a mold. Applied heat and pressure cause the beads to merge to form the panel shape. Individual beads are closed cells but there are sizeable open spaces between the beads. For reference, a common example of EPS is Styrofoam.
XPS is made by injecting liquid polystyrene plastic into an extrusion mold which creates a foam panel. XPS insulation is also a closed-cell type but is denser than EPS. XPS is also typically considered to have a better insulation quality than EPS.
Polyurethane foam is a mixture of two chemicals known as isocyanurates and polyols. These two chemicals are usually injected into a flat fixture or mold. When they meet, the resulting reaction causes a rapid, steady expansion which fills the fixture and forms the panel.
Polyurethane Insulation Pros & Cons
Polyurethane’s greater heat resistant properties mean a refrigeration system doesn’t have to work as hard to keep inside air cold, which saves energy and, in turn, operating costs.
Any discussion of polyurethane or polystyrene must begin with R-value. Stated simply, R-value is the capacity of an insulating material to resist heat flow. The higher the R-value, the greater the insulating ability.
Polyurethane’s greater heat resistant properties mean a refrigeration system doesn’t have to work as hard to keep inside air cold, which saves energy and, in turn, operating costs. In fact, polyurethane panels typically have an R-value of 32 which meets or surpasses DOE regulations.
Other advantages include:
- Polyurethane foam permanently adheres to metal panels adding strength and reliability
- Superior moisture resistance due to polyurethane’s 97% closed cell content
- Maximum walk-in storage space because polyurethane foam allows for thinner walls in comparison to other foam choices
- Polyurethane is a thermoset material which means it won’t melt. Because of its ability to resist fire, polyurethane earns a UL Class 1 rating.
One of the most common disadvantages cited against polyurethane is that it loses R-value over time. Actually, both polystyrene and polyurethane experience some fall-off over the years. What’s frequently not taken into consideration is that, with polyurethane, this drop is usually due to the panel being exposed to the elements. However, in real world situations, polyurethane foamed panels are mostly encapsulated and not exposed to the elements.
Polystyrene Insulation Pros & Cons
Polystyrene panels may cost less than polyurethane and they are lighter and easier to handle. In addition, they provide good resistance to water and airflow.
However, polystyrene’s lower R-value results in increased operating costs over time. Wall thickness must increase for polystyrene to match polyurethane’s R-value which reduces available walk-in storage space.
Other polystyrene disadvantages include:
- Poor ultraviolet radiation resistance
- Poor resistance to chemicals including organic solvents
- Polystyrene panels can only use hard nose construction types with edges made from wood or high density foam rails. These edges are less insulating and don’t seal as thoroughly as soft nose in which the edges are made of the same polyurethane foam as the rest of the panel.
Conclusion
While you can spend less upfront for a walk-in with cheaper insulation, you pay for it in the end with higher operating costs. When planning your next walk-in, remember what’s inside really counts, so make sure you are using the most efficient solution for your business.
RELATED CONTENT
- Advertisement -
- Advertisement -
- Advertisement -
- Advertisement -
TRENDING NOW
- Advertisement -
- Advertisement -