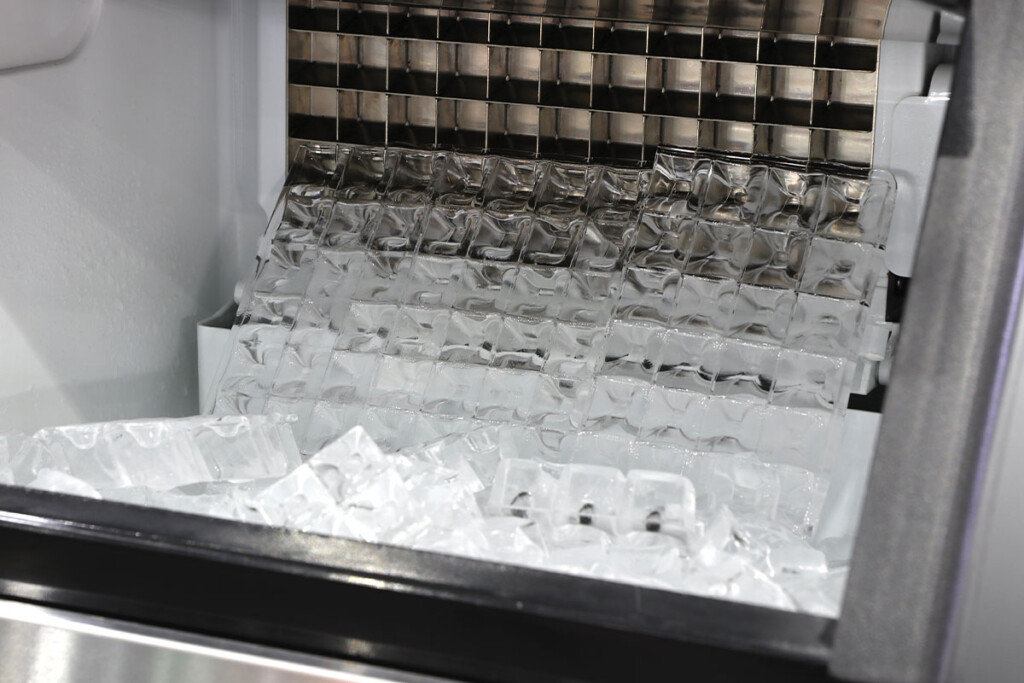
Years ago, when Cedric Cartiaux was new, he went on a call with his lead technician to repair an ice machine. “We set out to replace the thermal expansion valves,” says Cartiaux, service manager for CKI Service Group in Canton, Ga. “I had been out there the week before when the operator made the initial call that his ice machine wasn’t making ice. I adjusted the float switch, which got the unit making ice, but as I watched it work I noticed it was only dropping two-thirds of what it was capable of. The middle copper line wasn’t frosting like the other two, and the temperature split across the valve was high. Those are the signs that point to a bad thermal expansion valve. It seemed like a pretty straightforward diagnosis.”
On the return trip with parts, the lead technician decided to isolate and leak-check the unit, rather than diving straight into the more complicated thermal expansion valve replacement. After finding the system was leak-free, they were ready to reconnect the piping in front of the evaporator coil. “It was six connections, and the lead tech bet me he could do it all with one stick of solder,” Cartiaux says. “Standing on the ladder, just as we got to the last coupling, alarms blared, and water flooded the kitchen. It turned out the heat from the torch was too much for the sprinkler system.”
Having determined no leak in the unit, it was clear the repair of the thermal expansion valve was needed to get the ice machine back in optimum working condition. But with water in the equipment, there was nothing the technicians could do that day but clean up the mess and let the ice machine’s interior dry out completely. “We were both hoping nothing would short out,” Cartiaux says. “Since everything was disconnected for the repair, I knew we were probably safe, but if we turned it on with even the least little bit of water in it, we would probably end up replacing the control board.”
After letting everything dry, Cartiaux went back out and replaced the expansion valve. The now-dry machine started working at full capacity.
The Takeaway
Sometimes it takes multiple calls to get the right fix, even without the added disaster of the sprinkler system going off. “I was pretty sure it was just the expansion valve after watching the irregular frost pattern,” Cartiaux says. “But now that I’m the one in the supervisor position, I would have made the same call to double check for a leak before going through such a long and costly repair. The last thing you want to do is replace the expansion valve, only to find the machine still has a problem because of a leak you didn’t catch the first time around.”
RELATED CONTENT
- Advertisement -
- Advertisement -
- Advertisement -
TRENDING NOW
- Advertisement -
- Advertisement -
- Advertisement -