Heed Technicians’ Reach-In Reminders to Prevent Downtime
Keep your reach-in operating as intended with these bits of advice from Refrigerated Specialist Inc. and Clark Service Group.
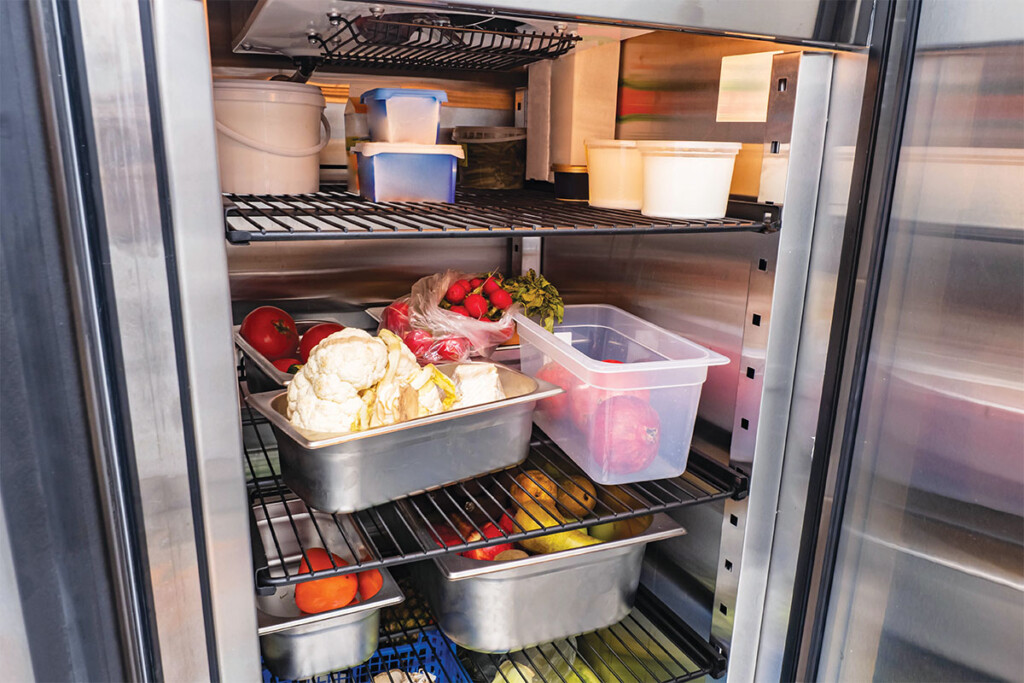
A dependably cool reach-in is central to many operations, but the units have their limits.
From overloaded units to improper use and installation errors, service technicians have stories—and solutions—to share.
Tag along as we share advice from Clark Service Group’s Kobi Patterson, service manager for the Central Pennsylvania area, and Scott Hester, president of Refrigerated Specialist Inc., in Dallas-Fort Worth/Greater Northeast Texas.
Here are some of their top recommendations:
Know your reach-in’s purpose. Importantly, Hester reminds of a reach-in’s equipment class. Designed for storage, reach-ins are not meant to manipulate product temperature, and operators shouldn’t attempt to manipulate unit temperature either. “Refrigeration systems only have ‘one speed,’” says Hester. “We often see operators treating temperature controls like the accelerator on a car, but setting thermostats colder does not make it cool faster.” Misuse like this can cause food temperature issues, not to mention a maxed-out thermostat.“Overall, lower settings or harsher treatment increases run time hours that triggers uptick in maintenance repair spend and shortens lifecycle,” Hester explains. He recommends regular, common-sense education at the staff level. Remind staff to only put food into the reach-in at proper temperatures, and avoid propping doors open as product is loaded.
Sidestep freeze-ups. Evaporator freeze-ups caused by overloaded product and/or blocked airflow marks an all-too-common yet completely avoidable mishap with reach-ins, shares Patterson. This error is especially troublesome with some energy-efficient units that cycle evaporator fans and compressors based on temperature setpoints.
“If they’re already suffering from low airflow, and then you’re completely shutting the fans off, later on, as they’re opening and closing that door while the fans are off, it’s just gathering more and more humidity and warm air from that opening and closing of the door,” explains Patterson, who notes the coil is still cold from the previous cycle. “That’s really just speeding up the process and the likelihood for freeze-ups to happen.”
But make no mistake: An energy-efficient unit isn’t the problem. Manufacturers spell out product capacities and airflow requirements; it’s just they aren’t always followed.
Less frequently, Patterson has seen boxes stacked on the top of a reach-in’s exterior, blocking airflow to the condenser—another no-no.
No matter the recipe that leads to a temperature issues, this is frustrating for technicians and operators alike. Once the reach-in is emptied of product and thawed, becoming unusable to operators, techs may spend time disassembling a unit only to find there’s nothing wrong with the reach-in’s components. And there’s an added frustration: “Manufacturers usually are not covering that under warranty,” says Patterson. “There’s nothing wrong with the unit; it’s just they’re not using it as intended.”
To keep in compliance, Patterson urges loading product per shift vs. loading for the whole day. Mind airflow at the interior back wall and, at the bottom of the interior, ensure staff is loading on an actual shelf vs. directly on the unit’s floor, he adds.
Mind the details. A properly placed and maintained unit is a multifaceted equation. A dedicated circuit is generally specified for reach-ins, notes Hester, and power cords should be kept off the floor to avoid unit damage and sparks. Also ensure the unit is level to keep it draining properly. Keep items like trash cans away from the air intake. Further, treat doors, drawers and gaskets gingerly, notes Hester. “This pays a dividend in lower costs of ownership over the life of equipment and adds years to life.” Hester also recommends maintaining daily temperature logs to indicate trends.
Finally, don’t underestimate the value of routine maintenance for reach-ins, says Patterson. Those planned checks allow techs to check condenser coils, filters, drains and gaskets, and can potentially help an operator avoid unplanned service calls down the line.
RELATED CONTENT
- Advertisement -
- Advertisement -
- Advertisement -
TRENDING NOW
- Advertisement -
- Advertisement -
- Advertisement -