Take Note of These Equipment Maintenance Tips
With a proactive approach, your operation may be able to sidestep an equipment breakdown.
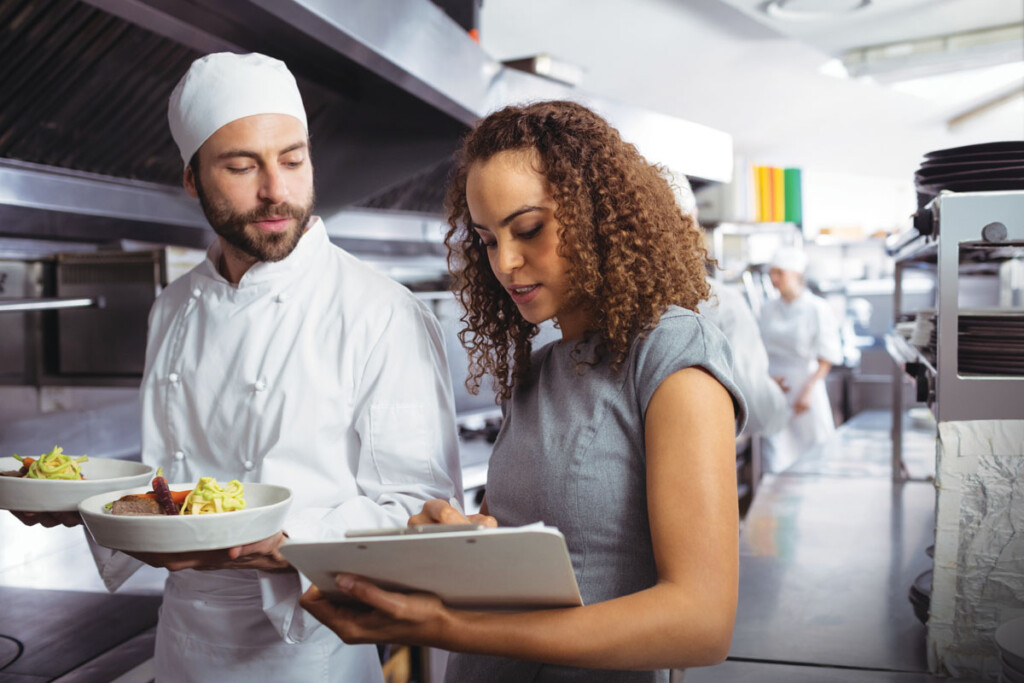
Time is often fleeting, but knowledge must not be.
As we embark on a new year and all the business planning that comes with it, we wanted to highlight some of the valuable time-and-money-saving knowledge we gained from 2021’s service stories.
Here, enjoy a bite-sized breakdown of three trends in service technician advice:
DON’T UNDERESTIMATE A “SMALL PROBLEM.” Steven Lokey, senior beverage technician for TWC Services, Jacksonville, Fla., told FER that “90% of service calls are something that’s a major issue that grew from a small problem.” Lokey recounted the story of a beverage dispenser yielding flat sodas at a local store. He checked all the normal suspects—the CO2 levels, the line to the carbonator tank and the ice bin—and was ultimately able to dispense a properly fizzy beverage. Yet within days, carbonated water was coming out of the store’s toilets, urinals and spigots. The problem? The check valve on the carbonator tank had failed, flushing carbonated water backward into the potable water lines. Lokey said the valve was probably malfunctioning little by little over time. While not in use overnight, carbonated water leaked out, making the day’s first pours flat. As more drinks were dispensed, carbonated water moved into the tank, resulting in fizzy drinks later in the day. Eventually, the tank suffered from total check valve failure.
SEE TRAINING THROUGH. Sure, you’ve probably trained the obvious employees, but don’t stop there. In 2021, FER heard two tales of well-meaning dishroom employees whose interactions with equipment caused failures. In one instance, multiple portable soup warmers failed before it was discovered that an employee was putting them through the dishmachine, soaking the equipment’s insulation and ruining its electrical components. In another instance, two employees’ differing water temperature preferences for a prerinse unit triggered a lockout on a new ice machine. One person used hot water and kept the cold-water valve closed, while another opened it just a smidge. “With the cold valve left open overnight [and no backflow preventer], the hot water migrated to the cold water in the pipes, which were the same pipes feeding water to the ice machine,” explained Jon Whitman, service manager, Arctic Food Equipment, Springfield, Mo. “On those nights when the ice machine turned on to fill up with water, the water in the line was hot enough to trigger the safety feature.” Once employees began shutting off both valves at day’s end, the lockouts ceased.
SPEND TIME, MONEY ON A PROPER INSTALLATION. You’ve likely heard it time and time again, but it bears repeating: Installation shortcuts can come back to bite you. This year alone, we heard three such scenarios, and our archives contain more. The most memorable one hailed from an assisted-living facility in Connecticut, where an overheated booster heater reportedly blew off the relief valve on a relatively new conveyor-type dishmachine. Issues continued and, after five service calls and several parts replacements, the service manager knew something else was to blame. A quick check of the building’s plumbing— something that should have been done during installation—pinpointed a hot water supply issue, but only after the equipment sustained undue wear and tear.
RELATED CONTENT
- Advertisement -
- Advertisement -
- Advertisement -
TRENDING NOW
- Advertisement -
- Advertisement -
- Advertisement -